Security takes clarity
No one can generate prosperity without someone providing protection. In times of accelerating change, protecting people, assets, and sovereignty is no simple task.
At Terma, we develop advanced technology and offer services and advice for a selection of application areas. We believe that a deep technical understanding paired with tight partner corporation produces superior security solutions.
Everything we do is aimed at preparing you to protect. Whether it be on live missions, in everyday operations, or in organizational and political decision-making, we help you to provide security.
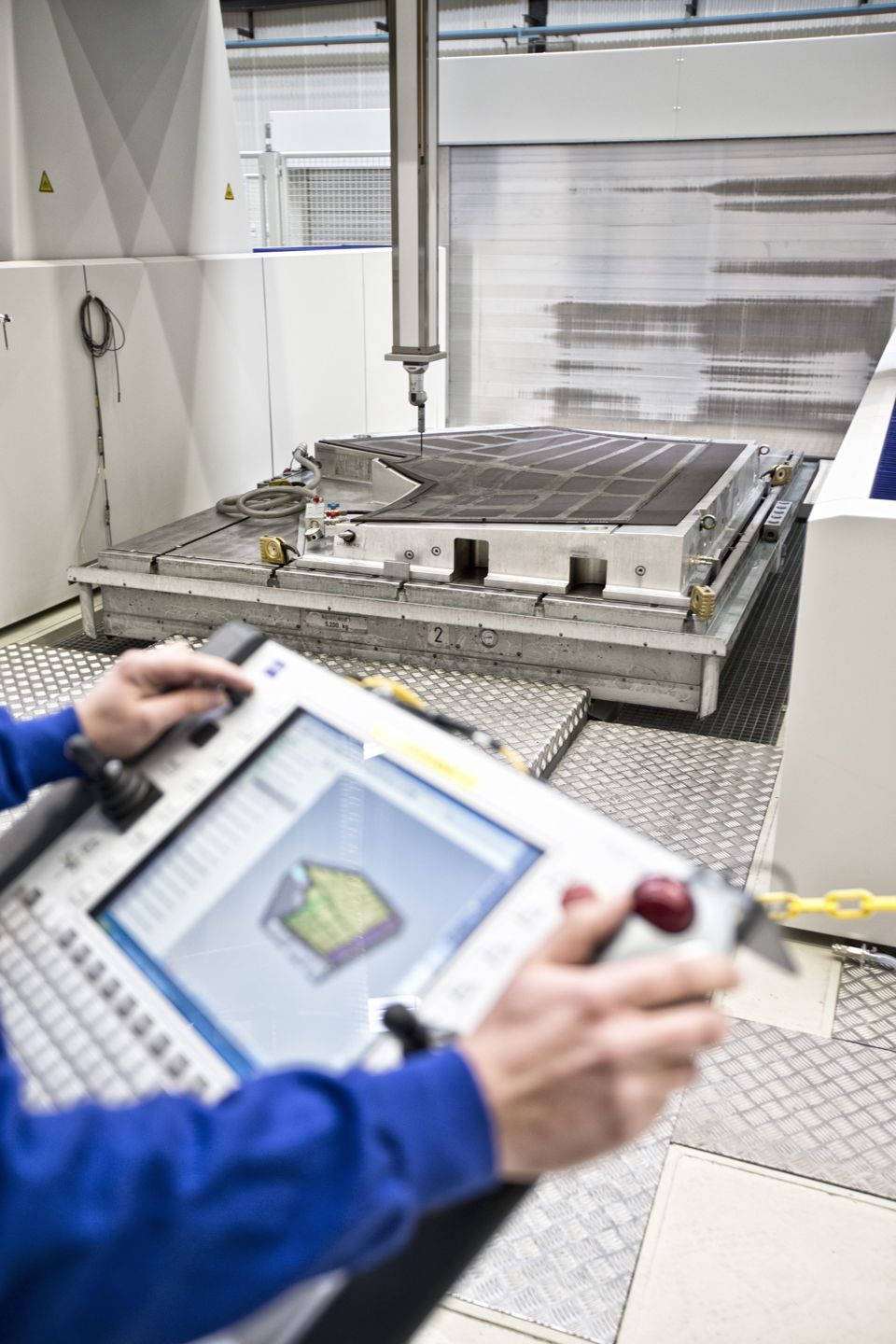
Technological excellence
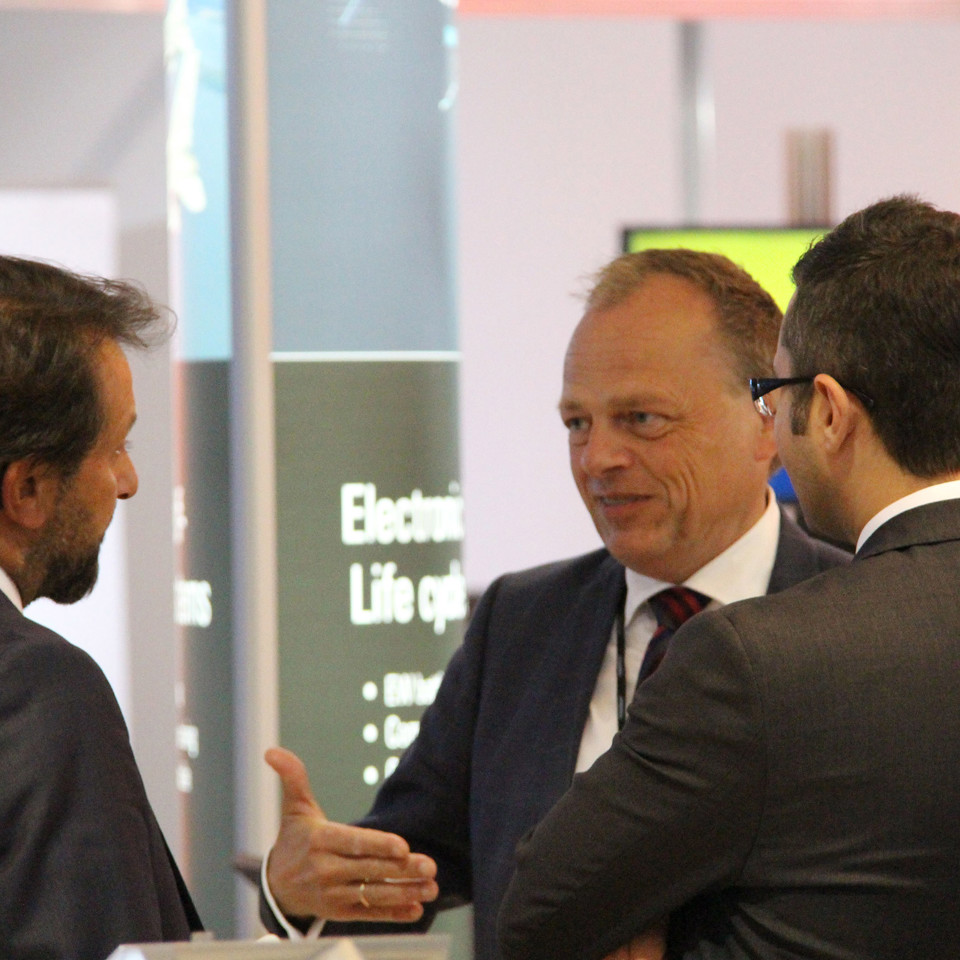
Partnership excellence

Sustainability and ESG
Our responsibility
At Terma, we believe that we have a responsibility for our business operations and the impact we have.
Learn about our Sustainability and ESG initiatives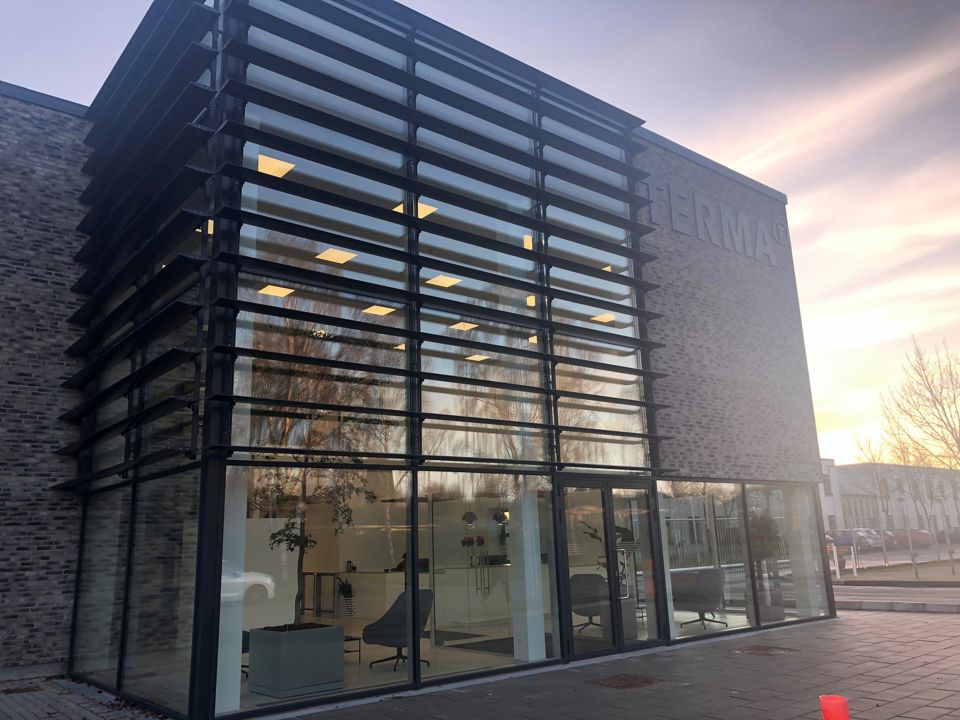
Our Company
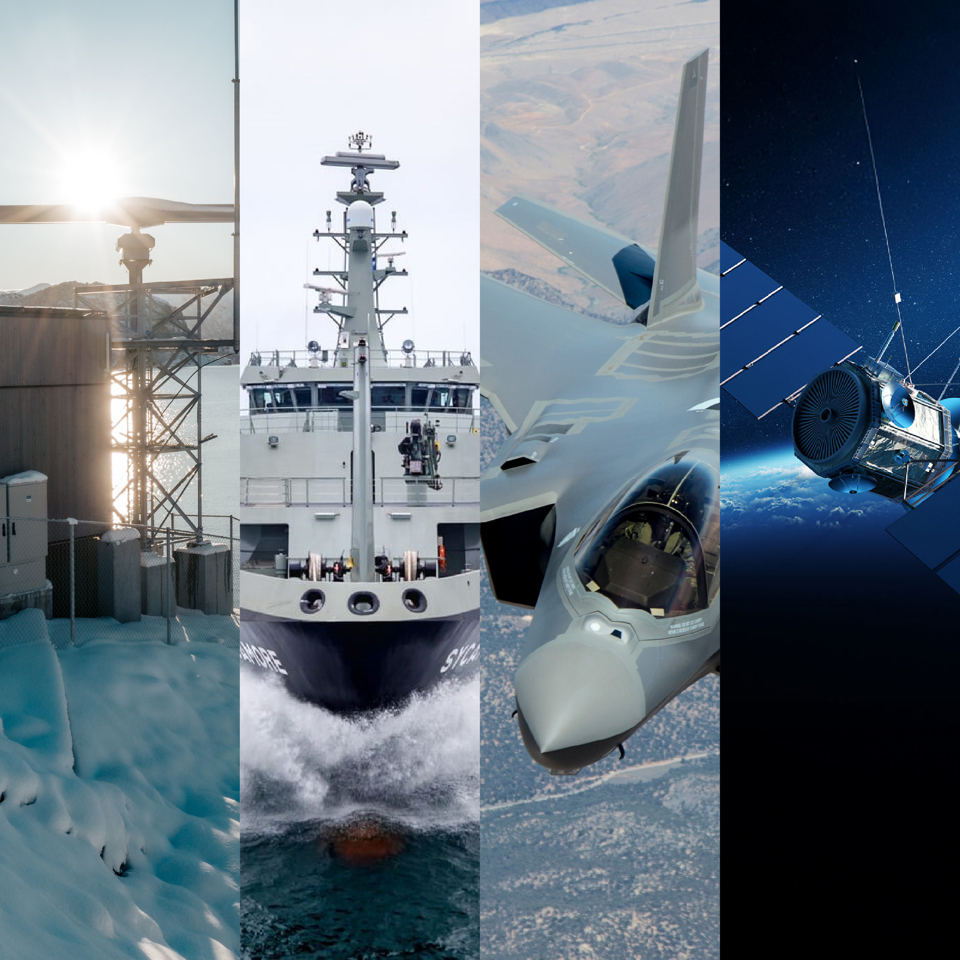
Our performance
Quality Management
Being a supplier of mission-critical solutions, we maintain a strict Quality Management System in order to fully satisfy customer requirements and needs. Consequently, we seek to be on the leading edge of the development within Quality Management.
Auditing and System Certifications
All major Terma locations are certified towards AS9100 (EN 9100) rev. D addressing the unique characteristics for these industry segments and including ISO 9001:2015. Further, most Business Areas are certified towards AQAP2310, AQAP2110, and/or AQAP2210.
Terma Aeronautics carries a certification in accordance with EASA Part 21 G from the Civil Aviation Administration of Denmark and Terma AS carries a Certificate of Accreditation EMAR21 subpart from the Netherlands Military Aviation Authority and a certification in accordance with EASA Part 21 J. Further, a number of special processes like Heat Treatment, Surface Treatment, Bonding of Composites and Non-Destructive Testing methods like Ultrasonic C-scanning, Dye Penetrant, and Digital X-ray have customer approvals against recognized standards. Terma Aerostructures has a Nadcap Accreditation for NonDestructive Testing Ultrasonic and a Nadcap Accreditation for Composites.